An array of packaging options is available for shields and contacts, including tape and reel, tray, tube and bulk. Laird packaging is Electronic Industries Association (EIA) 481 compliant. You can design small contacts requiring pick-up zones of 1 mm and weighing less than 0.01 grams.
• Popular tape and reel
• Plastic molded tray
• Tube packaging
• Bulk packaging
• 1 mm pickup zone
• EIA 481 compliant

We can help you automate applications of all forms of thermal interface materials. Laird offers automation solutions for dispensable gap fillers, printed thin-gap TIMs, and "robotic motion control" placed thick-gap TIMs.
- Robotic motion control
- In-line application
- Factory proven
- Printed thin-gap TIM
- Thick-gap TIM

We offer form-in-place gaskets using an automated system for dispensing conductive elastomers. Our resilient, form-in-place gaskets provide reliable protection for compartmentalized cast or plastic enclosures and packaged electronic assembles.
• Automated dispensing
• Form-in-place expertise
• Compartmentalized cast protection
• Plastic enclosure protection

Explore Laird’s vast array of custom precision metals products with counterbore-like features – from fingerstock gaskets to board-level shielding solutions to SMD grounding contacts. These custom solutions are thinner and lighter, helping you save space, and many ensure zero air gap. It’s our industry-leading quality, on-time performance and renowned engineering prowess that deliver the difference. We invite you to examine our quality certificates, then compare, save on TCO, and succeed.
● Hundreds of standard parts
● Rapid modifications produce custom designs
● Automated 100 percent coplanarity inspection system
● Innovative experts creating small, compact designs
● Resolve multiple issues by integrating metals with thermal/absorber materials
● PTC Creo, AutoCAD, Solidworks
Board-Level Shielding
Laird is a global leader in board-level shielding which effectively blocks unwanted waste energy for surface mount applications in countless devices.
Whether it is a one-piece shield, a multi-compartmental or deep draw shield or precision contact, Laird quickly designs and delivers best-value products offering maximum performance. Advanced laser welding and adhesive metal-joining technologies are just two recent innovations that enhance Laird’s board-level shielding solutions.
Laird’s expertise ensures that parts perform in superior fashion while optimizing your application. We use the latest systems to develop part designs in just hours.
● Many standard board-level shields meet several off-the-shelf application requirements
● Most shields can be modified for your custom design
● Our shields are thinner, lighter, save space and enable zero air gap
● Coplanarity of 0.05 mm (depending on part size) allows less use of solder
● Automated 100% coplanarity inspection system
● In-line production process includes part formation, cleaning, assembly, inspection and automated packaging
● Laird ingenuity has produced design features such as rigid corners, removable pick bridges (where replaceable covers enable repairs), and ultra-low height (<1.0 mm) shields
● Our vertical integration capabilities combine precision metals with a dielectric insulation coating, a thermal interface material, and/or an absorber material, providing you with a complete solution in a single process design
Learn more about board-level shielding
Fingerstock Gaskets
Laird’s engineered metal fingerstock gasket solutions date back to 1938. We specialize in designing miniature thin strip metal parts in quantities ranging from thousands to millions of pieces. With nearly 4,000 standard parts, we likely have an off-the-shelf solution to meet your needs.
If a custom fingerstock gasket design is required, Laird’s engineering team works to maximize efficiencies in performance, cost and manufacturability from the beginning stages of an application.
● Many standard fingerstock parts meet off-the-shelf application requirements
● Standard fingerstock parts can be modified for your custom design
● We use advanced simulation capabilities to accurately identify potential design issues
● See our specialized fingerstock capabilities from design through manufacturing
Laird solves any fingerstock need:
High precision assembly
Heat staking (both hand and automatic)
Heat treating
In-house die and fixture manufacturing
Multislide equipment
Photoetching
Plating
Progressing die stamping
Prototype fabrication
Resistance welding
Riveting
Secondary fabrication
Wire EDM
SMD Grounding Contacts
Laird’s standard precision electronic contacts deliver complete solutions. Our contacts will ground, carry current and signals, and interconnect boards and devices. A wide variety of plating options enables maximum electrical current-carrying performance.
You achieve optimal performance even while resolving EMI in extremely small, complex devices. What else is important? Installed costs of Laird grounding contacts are lower with our tape and reel packaging.
● Many standard grounding contacts meet off the shelf application requirements
● Standard SMD grounding contacts can be modified for your custom design
● Look to us for custom grounding or battery contacts and mechanical springs
● See our wide variety of plating options and array of standard format designs
● Our SMD grounding contacts satisfy each of your functional, assembly and packaging requirements
We prototype new, entirely customized designs for customers at incredible speed. You work with a local team, each engineer a part of our highly skilled design team based the world over and each using state-of-the-art design and modeling technologies.
• Rapid prototyping
• Design freedom
• Virtual prototype capability
• Medium or large production volumes
• PTC Creo, AutoCAD, Solidworks

Laird's highly advanced product modeling helps you define, oversee design, analyze and document your product under deveopment. Our predictive performance tools are noted for their ability to precisely forecast potential issues of concern and guide modifications.
• Rapid modeling concepts
• 2D/3DRF simulation (HFSS,CST)
• Program control
• Precise forecasting of issues
• PTC Creo, AutoCAD, Solidworks

Laird’s distinct advantages are broad. And proven.
- Rapid prototyping and global reputation for on-time delivery
- Renowned flexibility
- Application of leading software tools including PTC Creo, AutoCAD, and Solidworks
- In-house tooling designers and tool room allow for quicker turnaround time on prototypes
- High precision tolerances of wire EDM
Our people, processes, and technologies at Laird’s global prototyping sites have helped those locations (many ISO and IATF 16949 Certified) earn a reputation as true centers of excellence.
In the metals sector, we create solutions helping enable and protect electronics using precision thin gauge metal parts which are smaller, thinner, lower height, and lighter. For example, when a battery contact for automotive applications must have “flexing” requirements to withstand constant shock, design engineers regularly look to Laird for the exact end-to-end solution. You’re invited to learn about this and similar challenges – all of which we’ve resolved.
5 reasons to tap Laird’s prototyping expertise.
- Speed of development. We’re skilled at delivering rapid prototypes in days globally
- Reliability and performance. Predictive modeling capabilities readily available such as Finite Element Analysis (FEA), EMI modeling, and deep drawn simulations, along with accurate predictions of product lifetimes
- Low-cost designs. We make prototyping simpler for you and keep costs low
- Talented team. We employ experts with hundreds of years of combined experience
- Huge capital resources. Superior technologies to prototype and manufacture multi-functional protective solutions for electronic components. It’s the way forward.
We deliver. End to end.
Laird prototyping will help you achieve the optimum structural and EMI solutions to enable and ensure efficient product packaging and manufacturability. Contact our prototype experts in North America, in China or Asia, or Europe-Middle East-Africa.





Laird has a wide variety of sample kits available to assist customers in choosing the proper material for their needs. These sample kits aim to put products and data in your hands.

Rapid response that exceeds expectations is our continuous goal. Our request-for-quote delivery capability and speed of shipment performance receive constant senior management attention and action.
• Executive direction of RFQs
• RFQ delivery excellence
• Continuous process improvement
• Speedy shipments
• Regional localization

Laird is IATF 16949 certified. By placing a premium on quality, Laird has received the highest ratings on major customer qualification audits. Customers continually rank Laird among the top suppliers for quality and performance.
• Quality audit performance leader
• Customer preferred
• Complete customer experience management focus
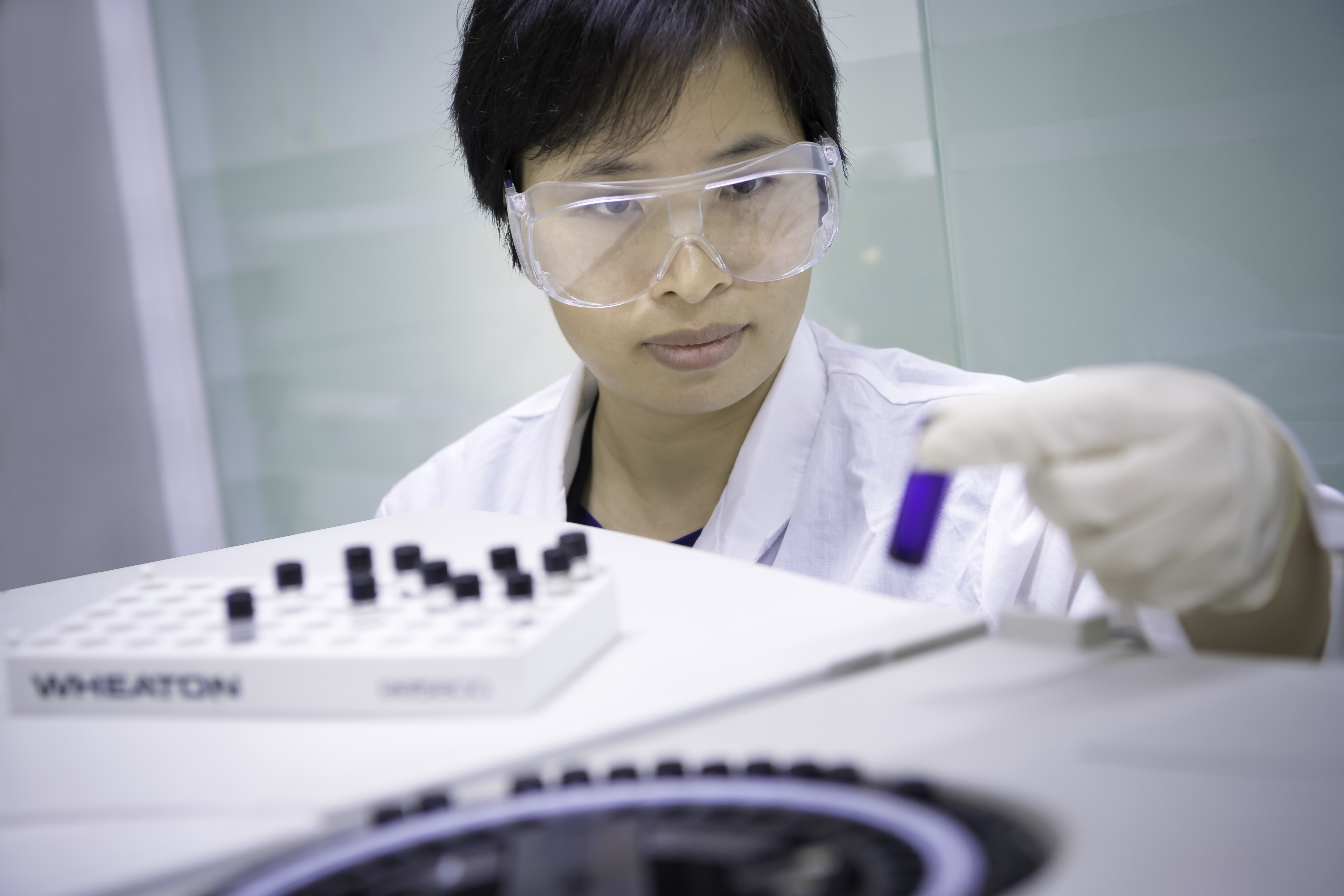
Laird's Virtual Design Centre is custom-built for design engineers enabling them to:
• Locate 2D and 3D parts, assemblies and library features
• Configure2D and 3D parts, assemblies and library features
• Download 2D and 3D parts and library features
Download your Virtual Design Centre here.

Partnering with us, you accelerate innovation to make our world intelligently connected.
We are designers helping designers. Manufacturers helping manufacturers. We help you avoid wasted effort and costs and thus speed the time-to-market for your systems.
Using our global capabilities, your design engineering teams blend with ours seamlessly to jointly think ahead, resolving the most formidable design challenges imaginable.
Anticipating your growing needs spawns our distinct innovations and capabilities.
Read how our co-engineering product development, modeling, rapid prototyping and testing teams work each day to help you accelerate your innovation.
Examine how our historic roots in thin gauge stamped and formed precision metal components served your needs. Today Laird precision metals stand above the rest.
Learn too about our leadership in automated systems for dispensing conductive elastomers, our automated product packaging and Laird-developed automated application of all forms of thermal interface materials.
Service never comes last. Giving you excellent service is first and remains first.
Laird people and Laird capabilities are leading edge. They’ll keep you on top.